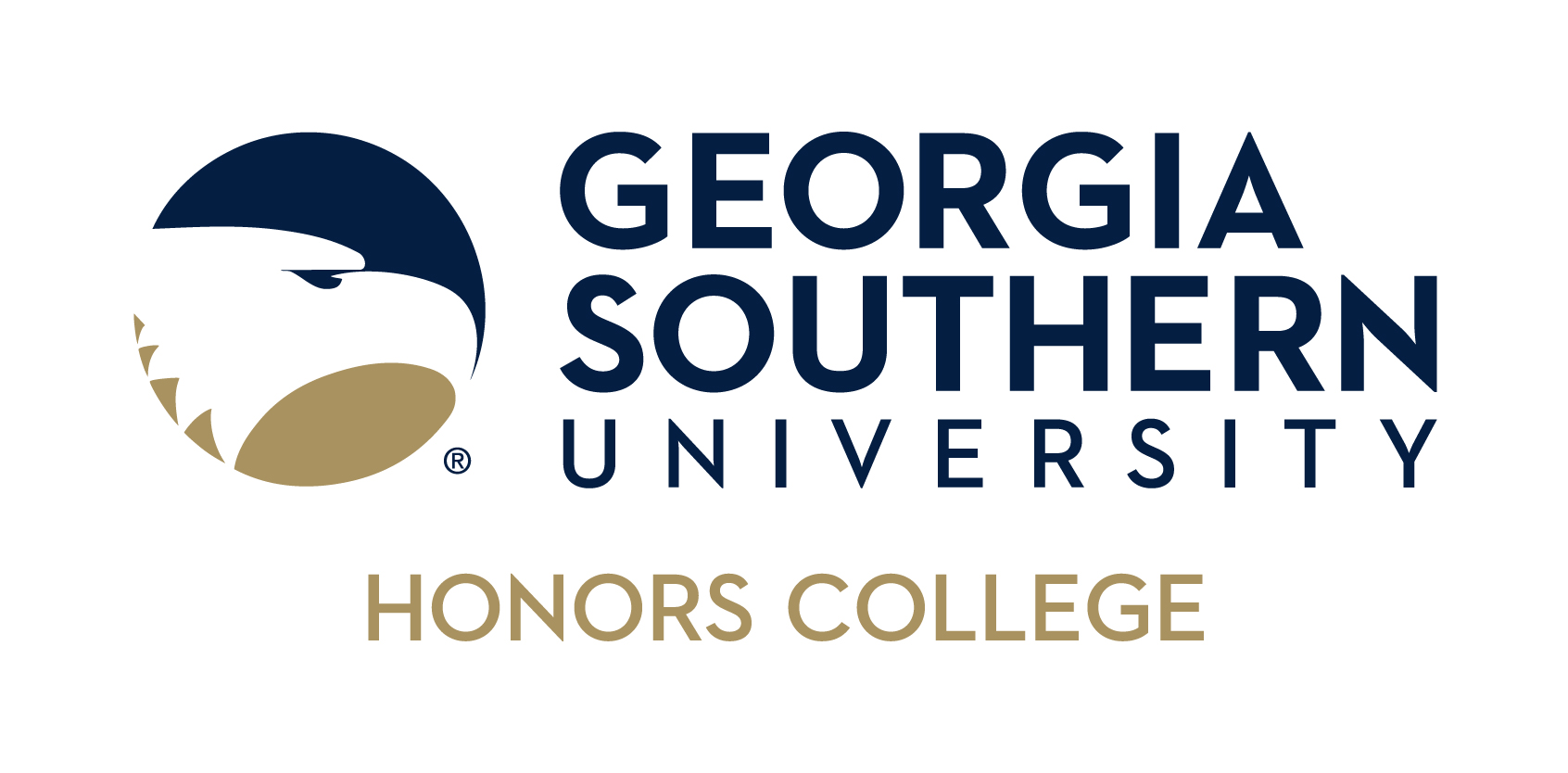
Honors College Theses
Publication Date
5-2-2023
Major
Mechanical Engineering (B.S.)
Release Option
Open Access
Faculty Mentor
Sevki Cesmeci
Abstract
Supercritical CO2 (sCO2) power cycles are superior to traditional water based, air-breathing, direct-fired, open Brayton cycles or indirect-fired, closed Rankine cycles in terms of efficiency and equipment size. They hold great potential in fossil fuel power plants, nuclear power production, solar power, geothermal power, and ship propulsion. To unlock the potential of sCO2 power cycles, utilized technology must withstand 10–600 MWe and at sCO2 temperatures and pressures of 350–700℃ and 20–35 MPa for nuclear industries. Amongst many challenges at the component level, the lack of suitable shaft seals for sCO2 operating conditions needs to be addressed. So far, conventional seals all suffer from the incapability of handling sCO2 pressures and temperatures in one way or another. These seals suffer from high leakage rates, bristle wear, and scalability constraints. There is a worldwide effort to develop effective sealing technologies for sCO2 turbomachinery. This research focuses on creating a proof-of-concept alternative seal design that can potentially be used in sCO2 turbomachinery. The seal will be demonstrated on a larger scale; utilizing water flowing through a chamber and studying how the pressure gradient and seal deflection affects the performance of the seal. Under these conditions, if the pressures at the top and bottom of the seal are constant and decreasing along the flow path, respectively, then the seal will deform in a way that forms a throat towards the root of the seal. In this work, an experimental methodology has been developed, including the instrumentation and fabrication of the components.
Thesis Summary
Supercritical carbon dioxide (sCO2) power cycles have recently emerged as a competitor to traditional water based, air-breathing, direct-fired, open Brayton cycles, or indirect-fired, closed Rankine cycles due to their efficiency and size. sCO2 holds great potential in existing power generation methods, but struggles to withstand the high temperatures and pressures the system is subjected to. This research creates a proof-of-concept alternative seal design that can be used in sCO2 turbomachinery through the creation of a larger scale test rig. The test rig went through multiple iterations until a reliable, efficient, and effective system was developed. The experimental methodology has been developed, including the instrumentation and fabrication of the components, and is ready for experimental trials.
Recommended Citation
Stuart, Cameron M., "A Proof-of-Concept Study for an Elastohydrodynamic Seal Design" (2023). Honors College Theses. 877.
https://digitalcommons.georgiasouthern.edu/honors-theses/877